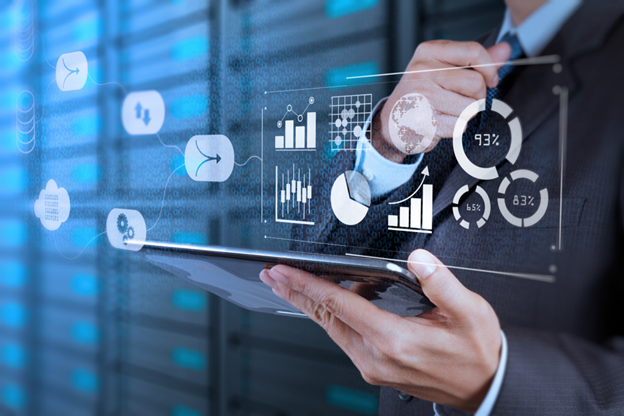
Assess Durability and Reliability of your products using Artificial Intelligence
Reliability is the probability that a product will perform without failing for a specific period. For instance, a refrigerator might have a 90% reliability over 5 years, meaning it has a high chance of working well without issues during that time.
Durability refers to how long a product can function as intended under normal usage conditions until it reaches a point where it no longer works (called a "limiting state"). For example, a washing machine might have a durability of 10 years
Save your time to calculate the value of Durability and Reliability for your products. In just a few minutes, get Artificial Intelligence calculated value of the Durability and Reliability of your product and according to standard EN 45552:2020 “General method for the assessment of the durability of energy-related products”
Enter the values in the empty fields and get your report
We have a special discount for bulk requests, get in touch with us in this case.
We can also customize special models to meet your different needs, just get in touch with us.
For values, you do not know, keep them empty. However, you recommend you to provide as much information as possible.
Details |
Your Answer |
|
Product Name |
|
|
Product and Usage Information |
||
1. Product Description |
Detailed specifications of the product. |
|
What is the Material Composition? Information about the materials used in the product. |
|
|
What is the primary function of the product*? |
|
|
What are the secondary and tertiary functions of the product*? |
|
|
Environmental and Operating Conditions |
||
2. Environmental and Operating Conditions |
Normal environmental conditions (temperature, humidity, , Exposure to chemicals, radiation, and other environmental factors, etc.). |
|
What are the normal operating conditions for the product? e.g., electrical stresses, mechanical stresses, typical use patterns and cycles, Operating stresses like electrical loads, mechanical loads, and thermal loads, Frequency and intensity of use (e.g., hours of operation per day), etc.) |
|
|
Any known variations or extremes in these conditions. |
|
|
Failure Definitions and Data |
||
3. Failure Definitions and Data |
Definitions of what constitutes a failure (failure modes and mechanisms). |
|
Historical failure data, including time to failure (TTF) data. |
||
Failure rates and modes for all relevant components and subsystems. |
|
|
What are the critical failure modes and mechanisms for the product? |
|
|
Maintenance and Repair Information |
||
4. Maintenance and Repair Information |
Details of maintenance actions and schedules. |
|
Repair actions and procedures. |
|
|
|
Repair Histories: Information about past repairs, including types of repairs, parts replaced, and frequency. |
|
Information on the durability of components and the product as a whole. |
|
|
Historical maintenance and repair records. |
|
|
What is the expected maintenance schedule for the product? |
|
|
Is the product repairable, and if so, what are the common repair actions? |
|
|
Stress and Damage Modeling Information |
|
|
5. Stress and Damage Modeling Information |
Stress analysis data (types, magnitudes, and locations of stresses). |
|
Damage models used for predicting wear-out failures (e.g., Information on the specific damage models (e.g., Arrhenius, Inverse power law) applied in durability analysis). |
|
|
Acceleration factors for accelerated life testing (ALT) conditions. Empirical data or calculations used to relate accelerated test conditions to normal use conditions*. |
|
|
Reliability Assessment Information |
||
6. Reliability Assessment Methods |
Any existing reliability testing data. |
|
Methods used for reliability assessment (e.g., FMEA, FMECA, Fault Tree Analysis*). |
|
|
Sample sizes and statistical methods used in testing. |
|
|
Product Life Cycle Information |
||
7. Product Life Cycle Information |
Expected product lifecycle stages (use, maintenance, repair, transport, storage). |
|
What is the expected operational lifetime of the product*? |
|
|
What are the usage and wear-out patterns of the product? |
|
|
Additional Information |
||
8. Additional Sources of Information |
Experience from similar products. |
|
Manufacturer constraints and specifications. |
|
|
Regulations and standards applicable to the product. |
|
|
User experience and feedback. |
|
|
Are there industry standards or regulations that dictate specific units for reliability? |
|
|
What units are commonly used for similar products in the industry? |
|
|
Data Specifics |
||
9. Component Reliability Data |
Failure rates of individual components. |
|
Mean Time Between Failures (MTBF), Mean Time To Failure (MTTF), Mean Time To First Failure (MTTFF) data. |
|
|
What kind of reliability data is available or can be collected for the product? |
|
|
10. Field Data and Test Results |
Results from field data and previous reliability tests. |
|
Data from accelerated testing conditions. |
|
|
11. Statistical Information |
Confidence intervals for failure rates. |
|
Statistical analysis methods used for data interpretation. |
|
|
What statistical methods will be used to analyze reliability data? |
|
|
Practical Considerations |
||
12. Practical Considerations |
What units will be most meaningful to the end-users of the reliability data? |
|
What units will provide the most actionable insights for improving product reliability? |
|
Definitions:
1. Limiting Event: This is an occurrence that causes the product to stop performing its main function. Examples include a broken part or a significant drop in performance.
2. Primary Function
Primary Function refers to the main purpose or the core function that a product is designed to fulfill. This is the reason why the product exists in the first place.
Example:
- For a washing machine, the primary function is to clean clothes.
- For a smartphone, the primary function is to enable communication through calls and texts.
3. Secondary Function
Secondary Function includes additional capabilities that enable, enhance, or support the primary function. These functions are necessary for the product to perform its primary function effectively.
Example:
- For a washing machine, secondary functions include the spin cycle to remove water from clothes, the ability to adjust water temperature, and different wash cycle options.
- For a smartphone, secondary functions include the touchscreen interface, the operating system that allows you to install and use apps, and the camera for taking photos.
4. Tertiary Function
Tertiary Function refers to other supplementary features that are not essential for performing the primary function but add value, convenience, or extra capabilities. These functions are often considered nice-to-have features.
5. Operational Lifetime refers to the total period during which a product or a component can perform its intended functions effectively and reliably under specified conditions of use, maintenance, and repair. It is a critical measure in understanding the durability and reliability of a product.
Examples of Operational Lifetime
- Light Bulb: An LED light bulb might have an operational lifetime of 25,000 hours, meaning it is expected to function effectively for 25,000 hours of use.
- Smartphone: A smartphone might have an operational lifetime of 3 to 5 years, after which it may start experiencing performance issues or become outdated in terms of software updates.
- Car: A car’s operational lifetime could be around 15 years or 200,000 miles, depending on factors like usage, maintenance, and driving conditions.
6. Acceleration Factors
Acceleration factors are used in accelerated life testing (ALT) to predict the life expectancy of a product under normal usage conditions. By subjecting the product to increased levels of stress (such as higher temperatures, voltages, or mechanical loads), failures can be induced more quickly, allowing for the estimation of product life under normal conditions. The acceleration factor is a multiplier that relates the time-to-failure under accelerated conditions to the time-to-failure under normal conditions.
7. Failure Modes and Effects Analysis (FMEA)
FMEA is a systematic method for identifying and analyzing potential failure modes within a system, their causes, and their effects on system performance. The goal is to prioritize the potential failures based on their severity, occurrence, and detection, and then take corrective actions to mitigate the risks. FMEA helps in understanding how and why a product might fail, and it is used to improve product reliability and safety.
8. Failure Modes, Effects, and Criticality Analysis (FMECA)
FMECA is an extension of FMEA that includes a criticality analysis. This analysis quantifies the risk associated with each failure mode by considering its severity and the likelihood of its occurrence. The criticality aspect helps in prioritizing the failure modes that need more urgent attention and resources for mitigation. FMECA is particularly useful in complex systems where the impact of failures can vary significantly.
9. Fault Tree Analysis (FTA)
Fault Tree Analysis is a top-down, deductive failure analysis method used to determine the root causes of system failures. The analysis starts with a top-level event (such as a system failure) and works backward to identify all possible causes, represented in a tree-like diagram. Each branch of the tree represents a possible cause or combination of causes that could lead to the top-level event. FTA helps in visualizing the pathways to failure and identifying the most critical components and failure modes.
10. Accelerated Testing
Accelerated testing involves subjecting a product to elevated stress levels to induce failures more quickly than under normal conditions. The goal is to obtain reliability data in a shorter time frame. Accelerated testing can include increasing temperatures, humidity, vibration, or other stress factors. The results are then used to predict the product's life and reliability under normal usage conditions by applying acceleration factors. Accelerated testing is crucial for identifying potential design flaws and improving product reliability before market release.